Bespoke Measurements
Your gateway to understanding and analysing full-field vibrations.
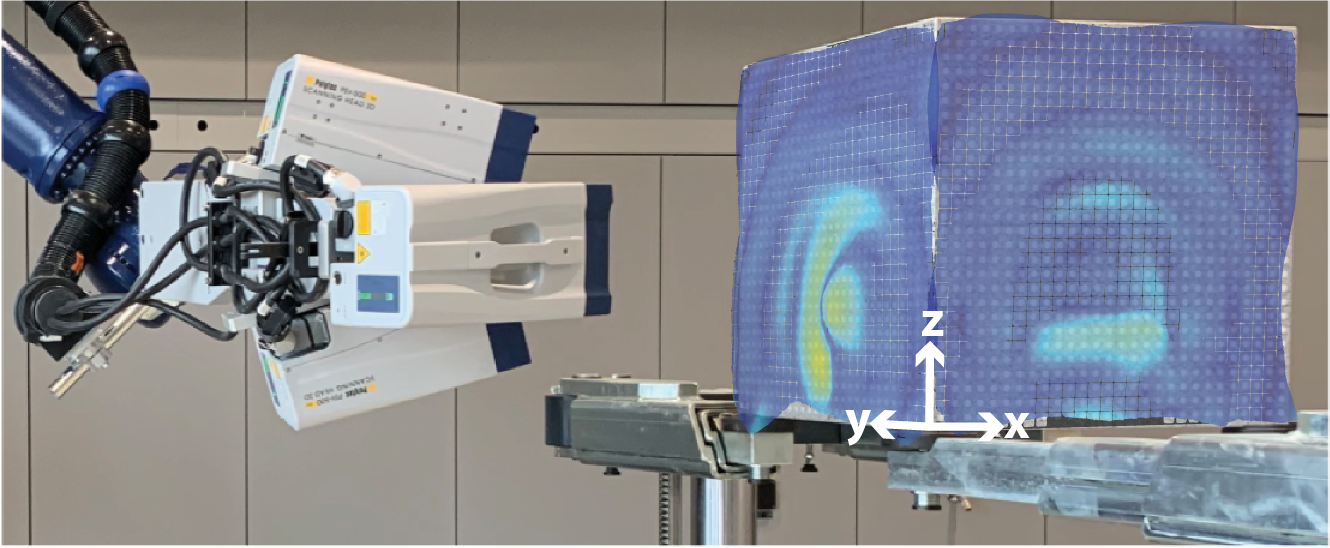
Robotized 3D Scanning Laser Doppler Vibrometer
At the "Centre for Immersive Wave Experimentation" we have gathered extensive experience in utilizing optical vibration measurements as part of our research. Such studies are invaluable in the fields of metamaterials, non-destructive testing, actuator characterisation, small-scale modelling, and geophysics – to name just a few.
In our laboratory researchers in industry and academia can unlock the dynamics of full-field vibrations in their projects.
Measurement laser: wavelength 1550 nm (invisible)
Targeting laser: 515 nm (green)
Geometry scan unit: wavelength 660-680 nm (red)
The LDV was last calibrated by Polytec to industry standards on 08.02.2023.
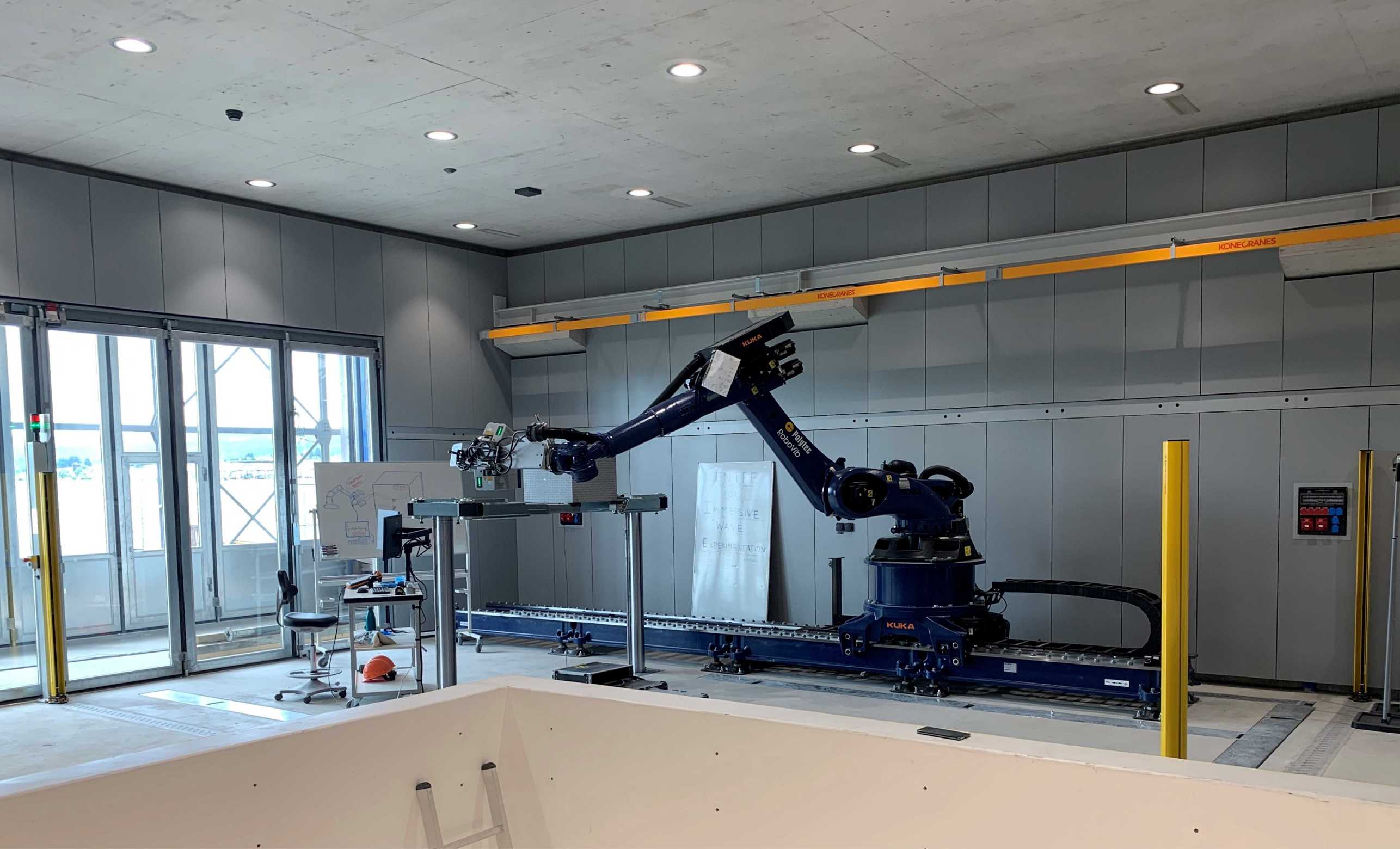
The measurement area of the 3D LDV spans 8 m x 3 m x 2.5 m (W x D x H). It is bounded by a light fence, allowing for longer automated measurements.
Structures up to 3 m x 3 m can be brought into the laboratory through a large gate.
Inside, objects can be supported by both a pit lift and crane, each permitting 5 tonnes of weight. Thus, enabling access to all sides of the target.
Selected Examples of Full-Field Scans
Here we list the advantages of laser Doppler vibrometery underlined by an assortment of example scans conducted in our laboratory.
Full-field Measurements
By robotizing the 3D LDV, we can capture the three component velocity vector across an entire surface, offering comprehensive data on the object's behaviour.

The robot is used to scan different sides of the target. Once these robot positions have been programmed the scanning procedure is fully automated and repeatable. At each physical measurement position a grid of points can be scanned at the desired spatial density.
Contactless Measurements
The LDV offers the ability to characterize wave propagation on highly mass-sensitive structures such as metamaterials through contactless measurements. Inaccuracies and complexities associated with mounting of contact sensors are eliminated. Furthermore, the LDV produces quantitative data on vibration frequencies, amplitudes, and modes.
Versatility in Testing Materials
The LDV can be used to assess a wide range of materials, such as metals, composites, ceramics, and 3D printed structures. Thus, making the LDV a versatile tool for non-destructive testing, allowing for the detection of minute defects or deviations in the material's integrity.
High Precision and Accuracy
The LDV provides incredibly precise measurements of surface vibrations without physical contact. Due to the superb spatial density and data fidelity, the data can be used for simulations and model updating.
Additional Laboratory Equipment
Our lab also offers a wide variety of actuation possibilities.
- 3-component piezoelectric actuators (external page PICA Shear Actuators)
(1x P-123.01, 1x P-123.03, 60x P-143.01, 1x P-143.03, 1x P-153.03, 3x P-153.05)
- 2-component piezoelectric actuators (PICA Shear Actuators)
(1x P-112.03, 1x P-122.03, P-142.03)
- 1-component piezoelectric actuators (PICA Shear Actuators)
(5x modified single stack PIC255, dimensions 5 x 5 x 3.5 mm)
- Impact source (pendulum and magnetic ball drop)
- Pulsed laser source (external page Q-Smart 450, 10 Hz)
These piezoelectric actuators can be driven via the signal generator of the LDV system or National Instrument's FPGA-based acquisition and control platform: FlexRIO FPGA.
Signal amplification is performed via:
- Single channel amplifier (external page TREK PZD350A M/S - bipolar configuration)
- 32 Channel amplifier (external page PD32 - PiezoDrive)
Please contact us if you would like to discuss how your project could benefit from LDV measurements. Scanning cost indication can be provided on a project by project basis.
Institut für Geophysik
Sonneggstrasse 5
8092
Zürich
Switzerland
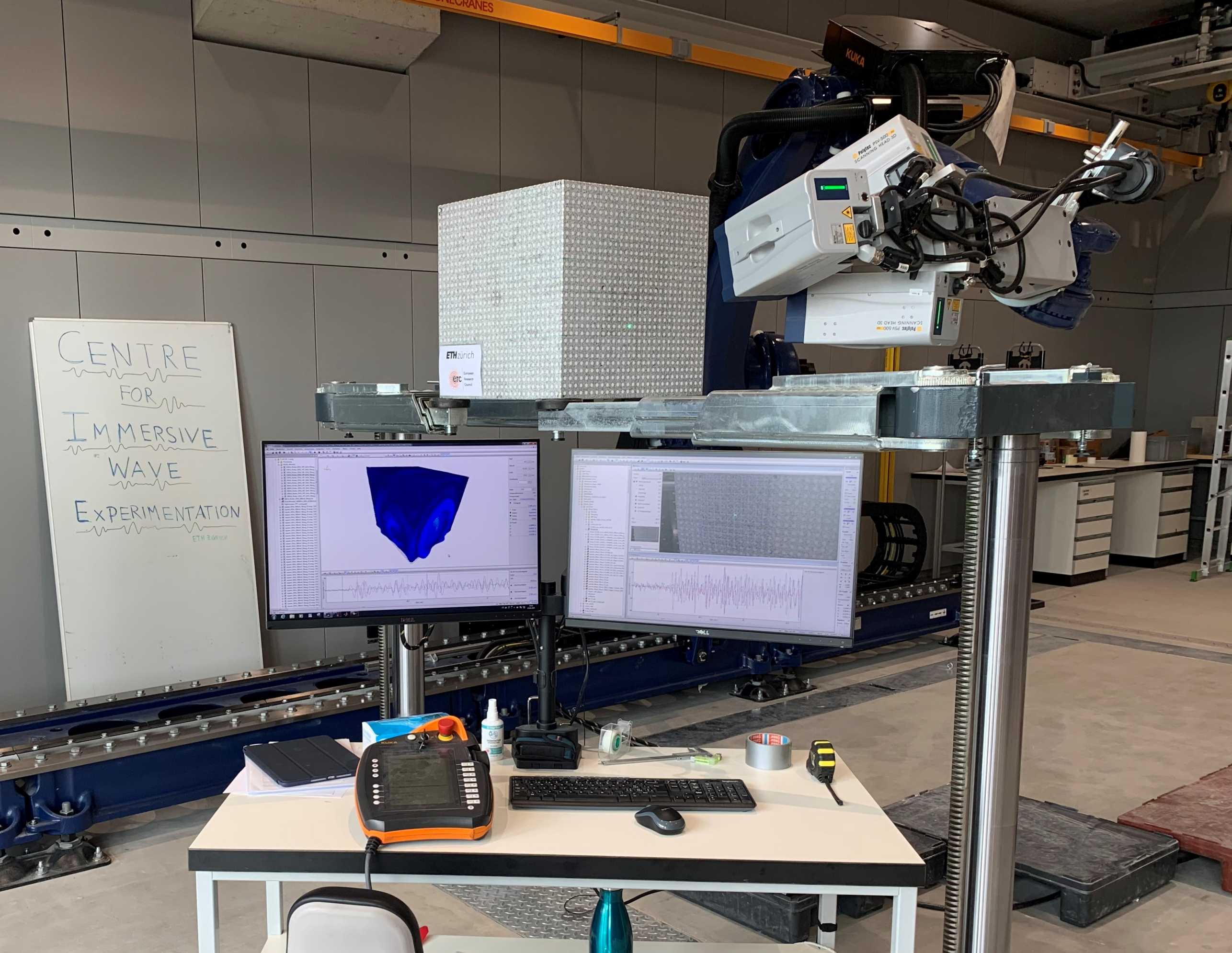